It’s becoming more expensive to build globally, and the construction industry is expected to feel the impact by 2025. Prices for core building materials are shifting again, and one big question is back on the table: are US import tariffs inflating building material prices, or is it more complicated than that?
With the return of proactive US trade policy impact under the Trump administration, many are wondering just how much tariffs affect what builders pay around the world. Let’s break it down and look at the numbers, the policies, and what they mean for your bottom line.
Global Building Material Price Trends in 2024–2025: What’s Going On?
Let’s break down what’s happening with global building material prices in 2025 under the Trump. Spoiler: they’re still high — but for different reasons depending on the material.
- Steel prices global: Up about 12% compared to last year. Demand from Asia is booming, and countries like China and India are tightening exports, which pushes prices up worldwide.
- Lumber prices global: No longer spiking like in the post-COVID years, but still sitting 20–30% higher than in 2019. Blame it on steady demand for new homes and supply chain issues caused by Canadian wildfires.
- Copper: Still pricey, but things are easing a bit as South American mines boost production.
- Cement: Mixed picture here — prices are rising in the EU, but pretty stable in places like Latin America.
- Plastics and insulation materials: Costs are rising, primarily due to fluctuations in oil prices and ongoing shipping disruptions.
So, what’s driving all this? It’s the usual mix of commodity price trends: insufficient supply to meet strong demand, higher energy costs, delays in global logistics, and even weather events disrupting things in some regions.
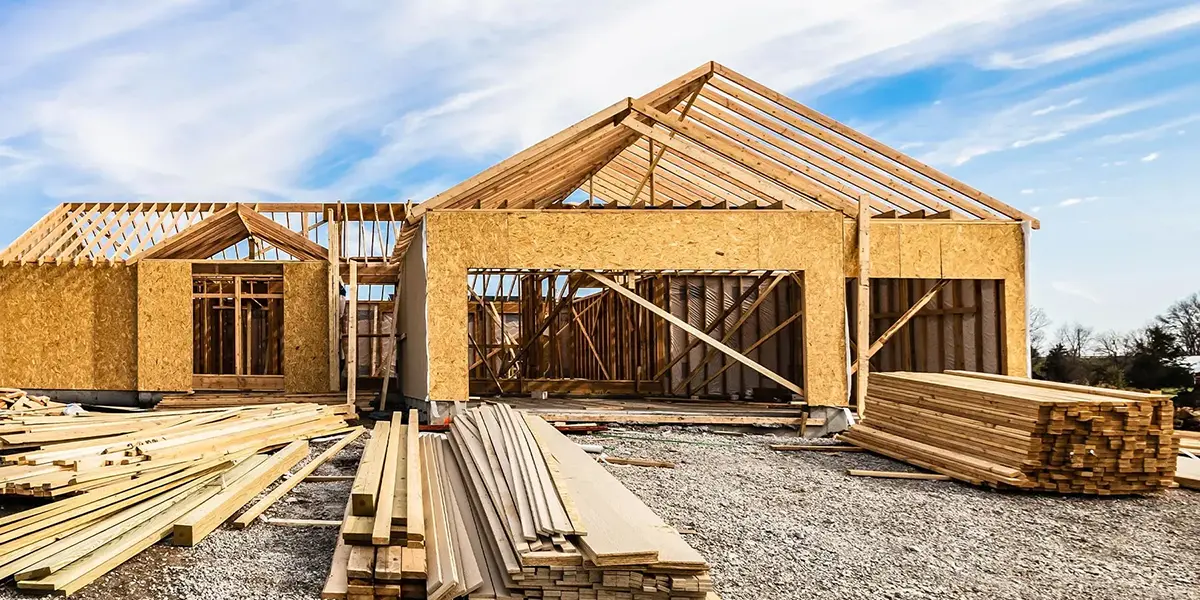
US Import Tariffs on Building Materials: The 2025 Picture
In 2025, the U.S. has doubled down on protective trade measures for construction-related goods. The list includes tariffs on:
- Steel and aluminum (25–30%)
- Canadian softwood lumber (20%)
- Chinese construction components and electronics (10–25%)
Targeted countries include China, Canada, and the EU — all major suppliers. The stated goals? Boost domestic production, protect jobs, and “reclaim industrial independence,” according to official briefings.
While those aims sound good on paper, the reality for global markets — and U.S. builders — is more nuanced.
The Link Explored: US Tariffs vs. Global Market Forces
So, how much do these U.S. tariffs really influence global building material prices? There are a few ways tariffs can ripple through the system:
- Higher U.S. demand for domestic goods can tighten global supply.
- U.S. buyers shifting to third countries drives up prices in those countries.
- Other countries retaliate or adjust their trade patterns.
But here’s the key: the U.S. isn’t the only game leader. The U.S. accounts for less than 10% of global steel consumption and approximately 5% of the worldwide lumber trade. Meaning? The steel tariffs global effect is real — but not dominant.
Asia, particularly China and India, continues to drive the market with its rapid growth in infrastructure. Add in fluctuating oil prices and logistics headaches, and it’s clear that U.S. tariffs are just one thread in a bigger web of global construction economics.
Impact on US Construction Costs and Housing Affordability
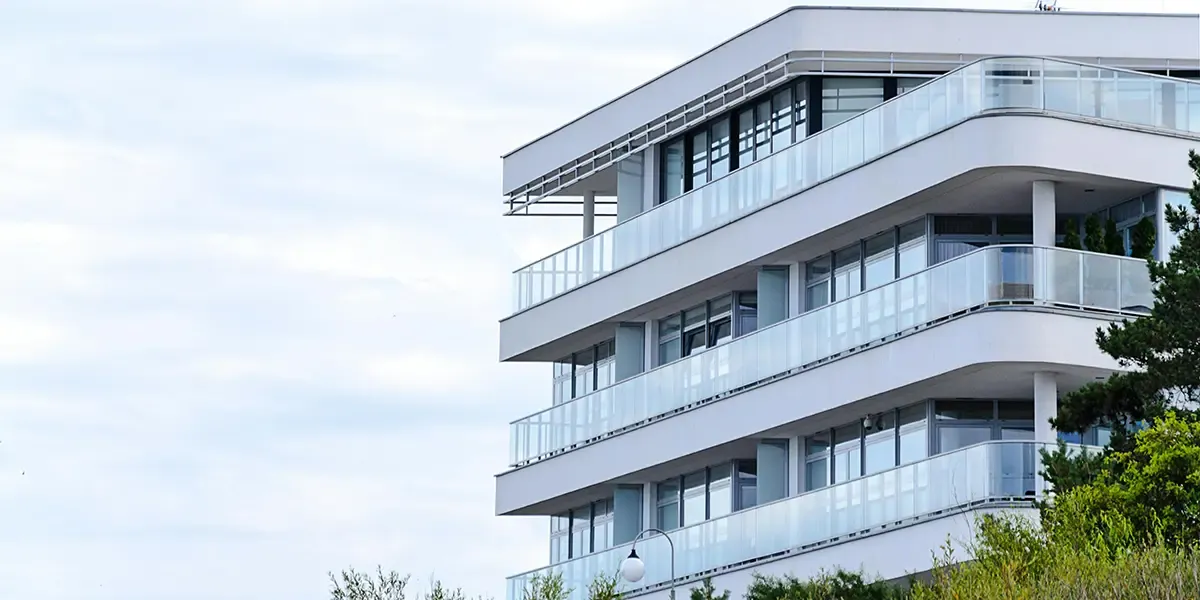
Now let’s talk about home. What do these pricing dynamics mean for construction costs 2025?
Short version? It’s more expensive to build. In the U.S., builders expect costs to rise by 8–15% on average for mid-sized projects — mostly due to higher material costs. That hits especially hard in affordable housing, where budgets are already tight.
But the tariff impact on real estate isn’t just about cost. Higher prices can lead to project delays, budget cuts, or even cancellations because no one knows what materials will cost next month.
The takeaway? When materials are more expensive, houses and apartments become less affordable.
Industry Adaptation and Supply Chain Adjustments
The good news? The industry isn’t sitting still.
- Developers are turning to alternative suppliers in Mexico, Vietnam, and South Korea.
- The construction materials supply chain is becoming more flexible — with localized warehousing, longer lead times, and risk-sharing contracts.
- There’s also a growing push for material recycling and reuse, which helps buffer some price shocks and supports sustainability goals.
Some U.S. companies are now investing in manufacturing at home to avoid tariffs — a trend that could alter supply dynamics in the long run.
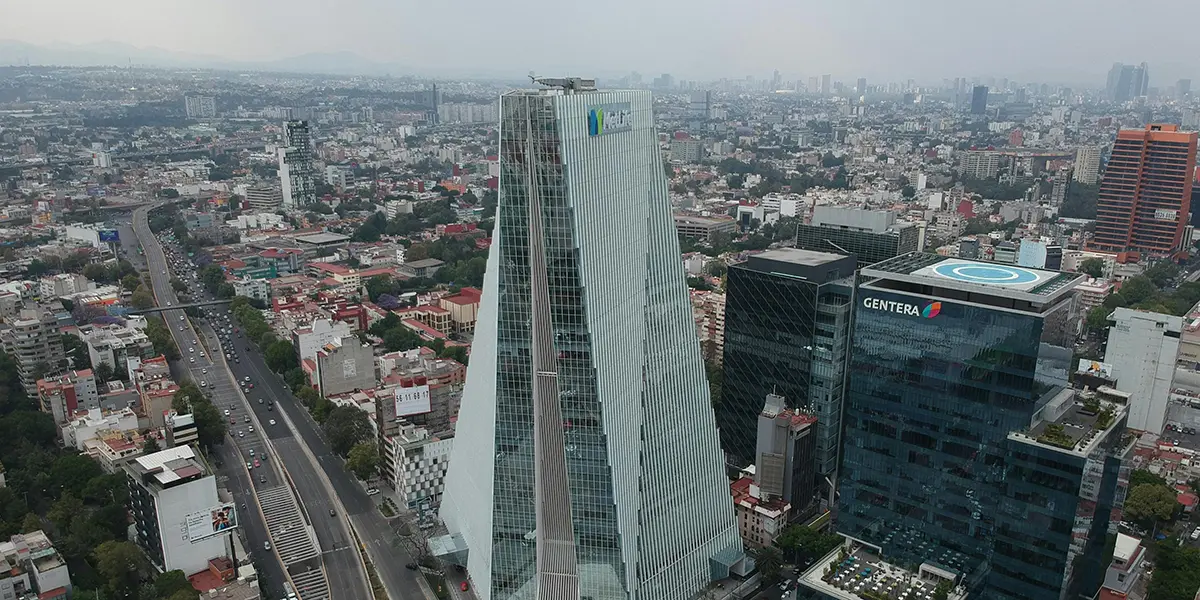
Conclusion: Are Tariffs Really Driving Global Price Changes?
Are U.S. import tariffs the chief reason global prices for building materials will be higher by 2025? No, not really. They contribute, yes, to what happens within the U.S. But they’re just a small part of a much larger picture. Prices come from factors such as global demand, energy costs, international politics, and climate change issues.
What should developers, contractors, and investors remember? Certainly keep an eye on tariffs — but that’s not all. Watch what’s happening with energy prices, global trade, and policy changes in other countries. In today’s world, everything’s connected, and no material cost goes up (or down) in a vacuum.